How a Distance Sensor Works: Understanding the Technology Behind Distance Measurement
Introduction
Distance sensors play a vital role in a variety of applications, from robotics and automation to parking systems and industrial monitoring. Whether measuring proximity, detecting obstacles, or mapping environments, distance sensors are essential components of modern technologies. Popular types of distance sensors include laser-based sensors, ultrasonic sensors, and infrared (IR) sensors. These sensors operate on different principles but all serve the same goal: to measure the distance between the sensor and an object.
In this blog, we’ll explore how distance sensors work, focusing on laser distance sensors, and explain why they are ideal for precise measurement tasks.
1. Types of Distance Sensors
Before we dive into how laser distance sensors work, let’s briefly look at other types of distance sensors. Each sensor type uses different methods to measure the distance between the sensor and an object.
1.1 Ultrasonic Distance Sensors
Ultrasonic sensors measure distance by emitting high-frequency sound waves. These sound waves travel until they hit an object, then bounce back to the sensor. By calculating the time it takes for the sound waves to return, the sensor can determine the distance to the object.
Use cases: Ultrasonic sensors are commonly used in parking systems, obstacle detection in robots, and liquid level monitoring.
1.2 Infrared (IR) Distance Sensors
IR sensors work by emitting infrared light and detecting the reflected light. The sensor measures the intensity of the reflected infrared light to calculate the distance to the object.
Use cases: IR sensors are often used for short-range applications like proximity sensing in consumer electronics or counting objects.
1.3 Laser Distance Sensors
Laser measure sensors use laser beams (light) to measure distances with high precision. These sensors are the most accurate and can measure distances over longer ranges compared to ultrasonic or IR sensors. This blog will focus on laser distance sensors, explaining their principles and why they are ideal for precision measurement tasks.
Use cases: Laser distance sensors are used in applications like industrial automation, 3D scanning, robotics, and automotive systems.
2. Working Principle of Laser Distance Sensors
Laser distance sensors are popular for their accuracy and reliability. These sensors work using two primary principles: time-of-flight (ToF) and phase shift. Let’s break down each principle to understand how they work.
Most laser measure sensors operate based on time-of-flight (ToF) measurement. Here’s how it works:
- Laser Emission: The sensor emits a laser pulse towards an object.
- Reflection: The laser pulse travels to the object, reflects off the surface, and returns to the sensor.
- Time Measurement: The sensor measures the time it takes for the laser pulse to travel to the object and back.
- Distance Calculation: By knowing the speed of light, the sensor calculates the distance with the formula: [
\text{Distance} = \frac{c \times \text{Time}}{2}
] Where ( c ) is the speed of light, and the time is the time taken for the pulse to travel to the object and back.
Advantages of ToF Technology:
- High Accuracy: ToF sensors offer millimeter-level precision.
- Long Range: Laser sensors can measure over long distances, from a few centimeters to hundreds of meters, depending on the model.
- Fast Measurement: ToF sensors provide quick readings, making them ideal for real-time applications.
ITOF Distance Measurement Principle vs DTOF Distance Measurement Principle
The iToF usually refers to the method of indirectly measuring the time of flight of light by modulating the emitted laser and analyzing the change of the relevant characteristics of the modulated laser after the propagation of a certain distance. This method is most commonly used for the analysis of the phase characteristics of the modulated laser.The phase information carried by the transmitted modulated laser and the modulated laser received after reflection will be different, and the phase difference can be calculated by analyzing the phase of the transmitted and the received phase. The actual propagation distance of the laser can be calculated by combining the phase difference information and the specified modulation frequency.
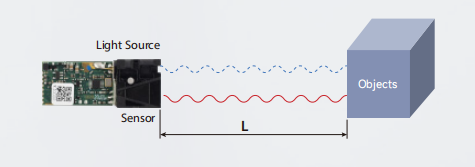
The dToF is a direct measurement of the time difference between transmitting laser and receiving laser, and inverse calculation of the distance of laser travel according to the speed of light. Based on the speed of light, this method requires the circuit related to the measurement of optical time of flight to have a very high reaction speed to improve the resolution of the measurement of time of flight, so as to improve the final ranging distance resolution. In view of the current technical level of the device, its distance division rate can be centimeter.
2.2 Phase-Shift Technology
Some laser measure sensors use phase-shift technology to measure distance. In this method, the sensor modulates the laser light at a known frequency. It then compares the phase of the emitted light with the phase of the reflected light. The phase difference provides the sensor with the information needed to calculate the distance.
Advantages of Phase-Shift Technology:
- High-Speed Measurement: Phase-shift sensors can measure distances very quickly, often in less than a millisecond.
- Stable Performance: These sensors are generally more stable and less affected by ambient light conditions.
However, phase-shift technology typically works best over shorter distances compared to time-of-flight sensors.
3. Factors Affecting Laser Distance Sensor Accuracy
While laser measure sensors are highly accurate, several factors can impact their performance and accuracy:
- Surface Properties: The reflectivity and texture of the object’s surface influence how well the sensor can detect the reflected laser beam. Smooth, highly reflective surfaces work best, while dark, rough surfaces can lead to measurement errors.
- Ambient Light: Laser sensors can sometimes be affected by ambient light, particularly in bright sunlight. Some sensors come equipped with features to minimize these effects.
- Sensor Alignment: Proper alignment of the sensor is crucial. Misalignment can result in inaccurate measurements or failure to detect the object.
- Distance Range: Laser sensors have a specified range within which they operate accurately. Going beyond the maximum range can result in incorrect measurements or no measurement at all.
4. Applications of Laser Distance Sensors
Laser measure sensors find applications across various industries due to their precision and versatility. Here are some common uses:
4.1 Robotics and Automation
Laser measure sensors are integral to robotics and automation. They help robots detect obstacles and navigate environments. These sensors are critical for applications such as autonomous vehicles and robotic arms, where precise movement is necessary.
4.2 3D Scanning
Laser measure sensors are widely used in 3D scanning to create digital models of physical objects or environments. The sensor measures the distance to multiple points on an object’s surface and helps generate a 3D representation.
4.3 Industrial Measurement
In industrial settings, laser measure sensors play a role in quality control, assembly line automation, and product testing. They can accurately measure the thickness, height, or distance of materials, ensuring consistency and quality in production.
4.4 Automotive Applications
In the automotive industry, laser distance sensors assist in systems like parking sensors and collision avoidance. These sensors help vehicles detect nearby objects and maintain safe distances from other cars.
Laser sensors, especially in LiDAR (Light Detection and Ranging) systems, are used for surveying and mapping large areas. LiDAR helps create detailed topographic maps and measure distances in outdoor environments like forests, cities, or geological sites.
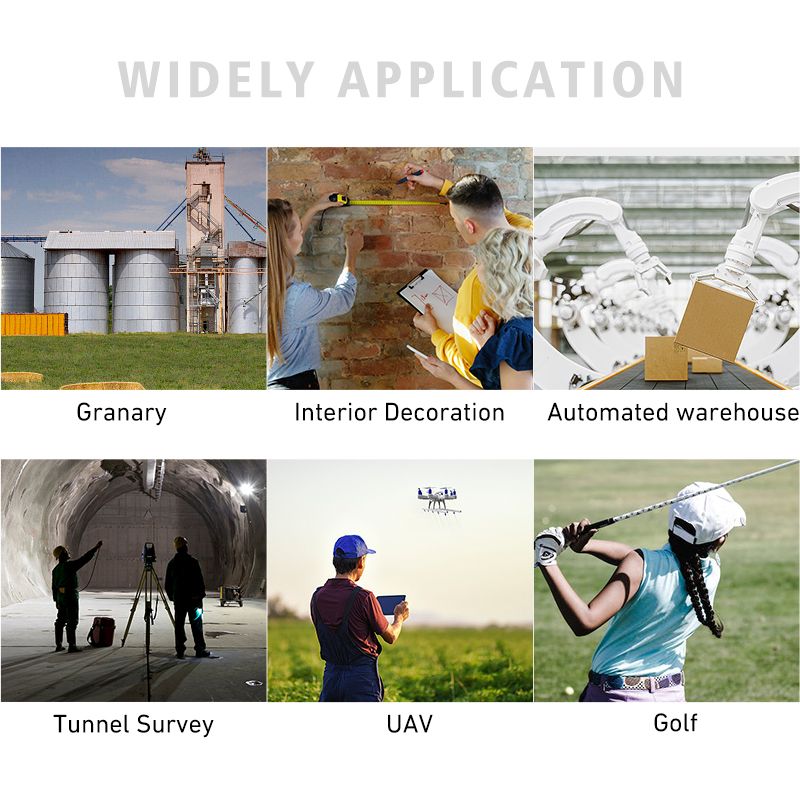
Laser measure sensors are powerful tools for accurate distance measurement, offering high precision and long-range capabilities. They use time-of-flight or phase-shift technology to calculate distances based on the laser’s travel time or phase difference. While factors like surface properties and ambient light can affect accuracy, these sensors still provide some of the most reliable and precise distance measurements available today.
Laser rang sensors have found their place in industries such as robotics, 3D scanning, industrial automation, and even automotive safety. As technology advances, we can expect these sensors to become even more compact, affordable, and capable, unlocking new possibilities in distance measurement and automation. Whether for high-precision measurements or obstacle detection, laser distance sensors are indispensable in many modern technologies.