Why Laser Rangefinders Are Critical for Modern Robotics
In the fast-paced world of robotics, industrial automation, and mechanical arm design, precision is non-negotiable. Whether it’s a robotic arm assembling microchips or an autonomous mobile robot (AMR) navigating a factory floor, the right robot sensors can make or break performance. Among these, laser rangefinders stand out as the gold standard for engineers seeking millimeter-level accuracy, rapid response times, and robust performance in harsh environments.
As a leading manufacturer of laser distance sensors, we’ve compiled the top reasons why industry professionals in robotics and automation are switching to laser-based solutions—and what you need to know to stay ahead.
Key Challenges in Robotics & Automation (And How Laser Sensors Solve Them)
1. Demand for Sub-Millimeter Precision
- Problem: Tasks like PCB assembly, welding, or pick-and-place operations require sensors to detect positions with micron-level accuracy. Traditional ultrasonic or infrared sensors often fall short.
- Solution: Laser rangefinders achieve ±0.1mm accuracy even at long ranges (up to 30m), ensuring robots perform delicate operations flawlessly.
- Use Case: A robotic arm using our LRF-X series reduced alignment errors by 92% in automotive battery module assembly.
2. High-Speed Operations Require Instant Feedback
- Problem: Slow sensor response causes delays in dynamic systems, like conveyor sorting or collaborative robots (cobots).
- Solution: Laser sensors offer 1ms response times, enabling real-time adjustments.
- Example: AMRs using laser-based obstacle detection navigate busy warehouses at 2m/s without collisions.
3. Harsh Environments Demand Durability
- Problem: Dust, vibrations, and temperature fluctuations degrade sensor performance.
- Solution: Our IP67-rated sensors operate in -20°C to 60°C conditions, ideal for foundries, CNC workshops, and outdoor AGVs.
4. Simplified Integration with Smart Systems
- Problem: Engineers waste time configuring incompatible sensors.
- Solution: Laser rangefinders with EtherCAT, RS485, or IO-Link interfaces plug directly into PLCs and ROS-based controllers.
- Pro Tip: Download our free SDK for quick integration with Universal Robots, Fanuc, and KUKA systems.
3 Industries Where Laser Sensors Transform Automation
🔧 Robotic Arms & Collaborative Robots (Cobots)
- Applications:
- Collision Prevention: Detect objects in a cobot’s path within 0.5° angular resolution.
- Tool Center Point (TCP) Calibration: Achieve repeatability of ±0.02mm for precision welding/painting.
🚚 Autonomous Mobile Robots (AGVs/AMRs)
- Applications:
- SLAM Navigation: Create real-time 3D maps with LiDAR-equipped sensors.
- Docking Accuracy: Guide AMRs to charging stations with ±2mm alignment.
🏭 Industrial Assembly Lines
- Applications:
- Quality Control: Measure part dimensions on moving conveyors at 1000 units/hour.
- Position Feedback: Ensure robotic grippers place components within 0.1mm tolerances.
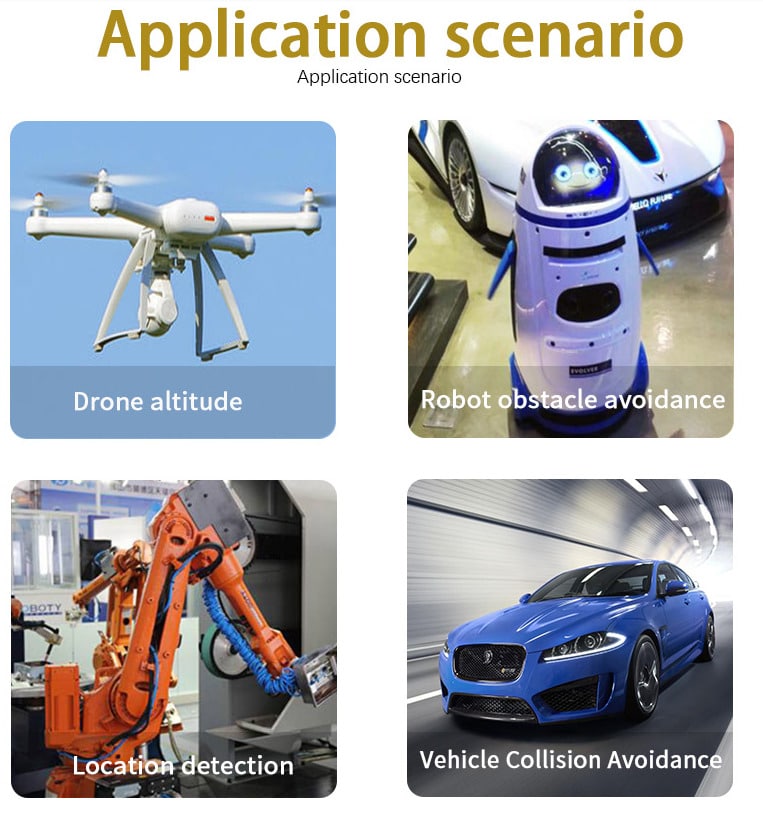
Cost vs. ROI: Why Laser Sensors Pay for Themselves
While laser rangefinders have a higher upfront cost than alternatives, their 20,000-hour lifespan and near-zero maintenance reduce downtime. For example, a food packaging plant saved $120k/year by replacing mechanical limit switches with non-contact laser sensors, eliminating wear-and-tear failures.
Need a Custom Solution? Let’s Engineer It Together
Every automation project is unique. Whether you’re building surgical robots or heavy-duty AGVs, our team offers:
- Free Sample Testing: Validate sensor performance in your setup.
- Customized Optics: Adjust beam divergence for narrow spaces.
- OEM Support: Modify housings or outputs to fit your design.
Explore Applications: Case Studies
Download Our Product Catalog: laser distan sensor
FAQ: Robots Sensors for Robotics & Automation
1.What are robot sensors, and why are they critical for robotics applications?
Robot sensors are devices that enable robots to perceive and interact with their environment. These sensors are crucial in robotics because they provide the data that allows robots to perform tasks such as navigation, object detection, and precise operation. Robots rely on sensors like laser rangefinders, cameras, and tactile sensors to ensure accuracy, safety, and reliability in various industrial, automotive, and healthcare applications.
2.How do robot sensors improve the precision of robotic arms in industrial automation?
In industrial automation, precision is paramount, especially in tasks like welding, PCB assembly, and material handling. Robots sensors, particularly laser rangefinders, provide millimeter-level accuracy, ensuring that robotic arms can perform delicate tasks with minimal error. For example, laser sensors enable robotic arms to align parts with exceptional precision, achieving repeatability as fine as ±0.02mm in tasks like tool calibration and assembly.
3.What types of robot sensors are commonly used in autonomous mobile robots (AMRs)?
Autonomous Mobile Robots (AMRs) rely on several types of robot sensors to navigate and avoid obstacles. Laser sensors (LiDAR) are among the most popular, providing high-precision measurements for SLAM (Simultaneous Localization and Mapping). AMRs also use ultrasonic sensors for proximity detection and cameras for visual processing, allowing them to safely navigate warehouse aisles and map environments in real-time.
4.How do robot sensors contribute to the safety of collaborative robots (cobots)?
Robot sensors play a vital role in ensuring the safety of collaborative robots (cobots) that work alongside human operators. Laser sensors, for instance, are used for collision prevention, detecting objects in the cobot’s path and allowing it to adjust its movements to avoid collisions. These sensors enable cobots to operate safely in environments where humans are present, enhancing productivity while minimizing the risk of injury.
5.What are the benefits of using laser rangefinders as robot sensors in high-speed operations?
Laser rangefinders are particularly effective in high-speed operations due to their ultra-fast response times (typically 1ms). These sensors can provide instant feedback to robots, allowing for real-time adjustments in dynamic environments like conveyor belts, sorting systems, and automated pick-and-place operations. This ensures smooth and continuous operation, even in fast-paced industrial environments.
6.How can robot sensors help with precision navigation and mapping in robots?
Robot sensors, particularly laser rangefinders and LiDAR, are essential for precise navigation and mapping. By creating detailed 3D maps of their environment, robots can effectively localize themselves and avoid obstacles. This is particularly important in autonomous mobile robots (AMRs) and AGVs, which rely on sensors to navigate complex environments, detect obstacles, and ensure safe navigation without human intervention.
7.What is the role of robot sensors in industrial assembly lines?
In industrial assembly lines, robot sensors are used for tasks like quality control, part inspection, and precise positioning. Laser sensors, for example, can measure part dimensions on fast-moving conveyors at rates of 1,000 units per hour, ensuring that each part meets the required specifications. Robots sensors also provide real-time position feedback to robotic grippers, ensuring components are placed within tight tolerances, such as 0.1mm.
8.How do robot sensors handle harsh environmental conditions in industrial settings?
Many robot sensors, especially laser rangefinders, are designed to withstand harsh environmental conditions, such as dust, vibration, and temperature extremes. Sensors with IP67 ratings are resistant to dust and water, making them suitable for use in environments like CNC workshops, foundries, and outdoor automated guided vehicles (AGVs). These rugged sensors ensure reliable performance even in challenging conditions.
9.How do robot sensors improve efficiency and reduce costs in automation?
While robot sensors may have a higher initial cost, they offer significant long-term savings by reducing downtime and improving efficiency. For example, laser sensors eliminate the need for mechanical components that wear out over time, such as limit switches. This reduces the frequency of maintenance and replacements, ultimately leading to cost savings. A case in point is a food packaging plant that saved $120k annually by switching to non-contact laser sensors, avoiding mechanical failures and minimizing downtime.
10.Can robot sensors be customized for specific robotic applications?
Yes, robot sensors are highly customizable to meet the specific needs of different robotic applications. Whether you need adjustments to beam divergence for narrow spaces, or specialized housings and outputs to fit your robot design, sensors can be tailored to your exact requirements. Manufacturers like Meskernel offer customized solutions, including free sample testing to ensure the sensors perform optimally in your setup.